Alfa Laval M line of gasketed plate-and-frame heat exchangers are used for high design pressure (>10 bar/145 psi), such as in carbonated beverages. The large range of plate and gasket types comply with Food Contact Materials (FCM) requirements for pasteurization and other heating and cooling duties in hygienic and utility applications in the dairy, food, beverage and pharmaceutical industries.
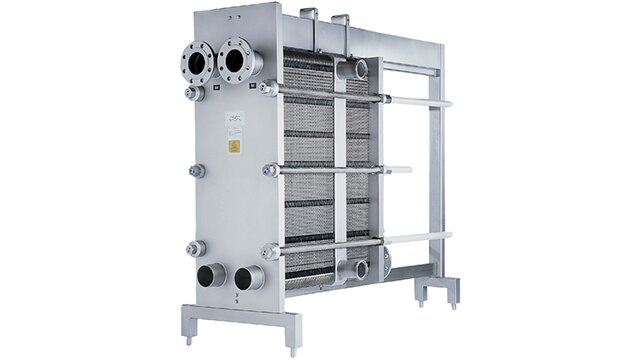
Competitive choice for high pressure hygienic processes and utility applications
- Engineered specifically for high design pressure
- High degree of service-friendliness – FDA compliant gaskets for easy opening, inspection and cleaning, and also designed for Cleaning-in-Place(CIP)
- Fouling resistance and thermal efficiency thanks to range of pressing depths and chevron patterns as well as various corrugations
- Flexible – heat transfer area can be modified by adding or removing plates or combining different plates and material if process parameters change
- Suitable for multi-section heat exchangers for pasteurization saving on space, piping and costs
Optimization of duties: M line heat exchangers are available in three different sizes and work with various plate types to ensure optimal performance for your application.
Plate types for different hygienic needs

Two different plate types are available for BaseLine & M Line:
- Chevron type plate pattern ensures good distribution of the product as well as high thermal efficiency and is used in a wide range of industries.
- Gemini double-wall plates ensure a fully mix-proof design. It consists of two plates pressed together and prevents cross contamination between fluids in case of leakage through the plates.
The chocolate pattern distribution area ensures that the fluids are evenly distributed across the entire plate to avoid stagnant zones that can result in fouling.
How it works
Channels are formed between the plates and the corner ports are arranged so that the two media flow through alternate channels. The heat is transferred through the plate between the channels, where the counter-current flow helps attain the highest possible efficiency. The corrugation of the plates provides the passage between the plates, supports each plate against the adjacent one and enhances the turbulence, resulting in efficient heat transfer. Our thermal design engineers will help you design and select the model and configuration that is suitable for your application needs while delivering maximum thermal performance and minimizing pressure drop.
Alfa Laval hygienic liquid/liquid GPHE
Alfa Laval multi-section pasteurizer GPHE
Multi-section hygienic GPHE
Features
Adjustable feet
Bearing box
Connection plate roller
Elongated nuts
Fixed bolt head
Key hole bolt opening
Lock washer
Pressure plate roller
Tightening bolt cover
Documents